Root Cause Analysis Part 1 Learn Lean Sigma

Root Cause Analysis Part 1 Learn Lean Sigma Root cause analysis (rca) is a critical component of the analyze phase of lean six sigma’s dmaic (define, measure, analyze, improve, control) methodology. rca’s primary goal is to identify the underlying cause of a problem or issue rather than simply treating the symptoms. understanding the root cause allows organisations to implement. Root cause analysis (rca) is a key tool in continuous improvement, acting as a systematic approach to identify and tackle the underlying issues behind problems. rca aims not only to provide a temporary fix but to offer long lasting solutions by addressing the root causes. rca, such as the fishbone diagram, the 5 whys, and fmea.

Root Cause Analysis Part 1 Learn Lean Sigma Root cause analysis is a range of tools and techniques used to address a problem in a business, we define a problem as the difference between what is happening vs what should be happening (an abnormal occurrence) e.g., product defects, late deliveries, processes not running at correct speed etc. the tools and techniques used in root cause. A root cause analysis (rca) is a problem solving method to identify the root causes of faults or problems. a factor is considered a root cause if removal from the problem fault sequence prevents the final undesirable event from recurring. short term actions are not profitable for the organization; thus, rca helps permanently eliminate the issues. The lean six sigma bureau offers a comprehensive range of training programs, from yellow belt to master black belt, equipping you with the knowledge and expertise to master rca and all.conclusion:root cause analysis is a powerful tool for uncovering the underlying causes of process problems and driving continuous improvement. Root cause analysis (rca) is such a simple concept that its genius is in its simplicity. basically, if you truly understand what is causing the problem, the solution is just waiting to be discovered. all seven steps given have a reason for making it into the root cause analysis template, as they all provide much needed and specific information.

Lean Six Sigma Root Cause Analysis Rca Vative The lean six sigma bureau offers a comprehensive range of training programs, from yellow belt to master black belt, equipping you with the knowledge and expertise to master rca and all.conclusion:root cause analysis is a powerful tool for uncovering the underlying causes of process problems and driving continuous improvement. Root cause analysis (rca) is such a simple concept that its genius is in its simplicity. basically, if you truly understand what is causing the problem, the solution is just waiting to be discovered. all seven steps given have a reason for making it into the root cause analysis template, as they all provide much needed and specific information. Root cause analysis for beginners, part 1 and part 2 (webcast) asq fellow jim rooney walks you through the basics of root cause analysis. quality revolution reduces defects, drives sales growth at 3m (pdf) case study looking at how 3m combined lean six sigma and a top 200 customer focus to improve its belt fabrication processes and reduce. The 6ms refer to six key inputs that contribute to process variation: machinery, manpower, materials, methods, measurement, and mother nature. categorizing causal factors into the 6ms provides an intuitive framework for structured brainstorming and analysis. the approach helps identify root causes by mapping relationships in an ishikawa.
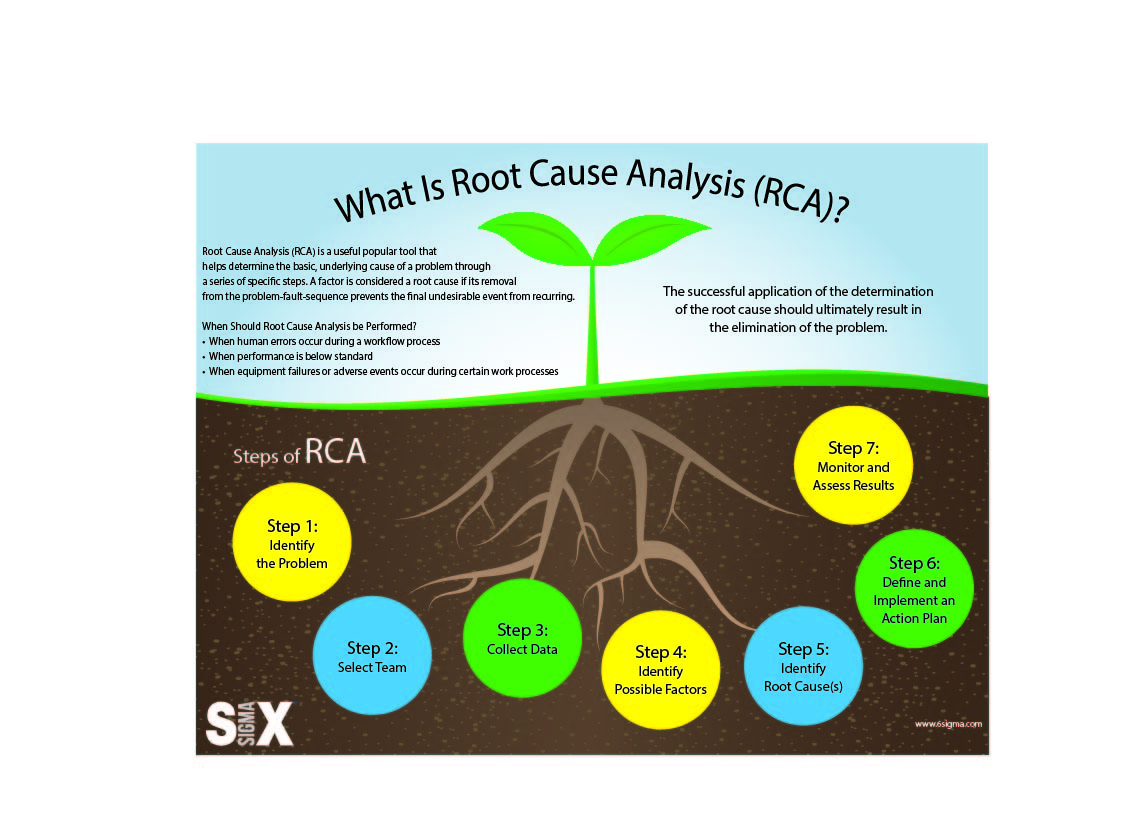
Infographic Root Cause Analysis Rca Lean Six Sigma Root cause analysis for beginners, part 1 and part 2 (webcast) asq fellow jim rooney walks you through the basics of root cause analysis. quality revolution reduces defects, drives sales growth at 3m (pdf) case study looking at how 3m combined lean six sigma and a top 200 customer focus to improve its belt fabrication processes and reduce. The 6ms refer to six key inputs that contribute to process variation: machinery, manpower, materials, methods, measurement, and mother nature. categorizing causal factors into the 6ms provides an intuitive framework for structured brainstorming and analysis. the approach helps identify root causes by mapping relationships in an ishikawa.

Lean Root Cause Analysis

Root Cause Analysis Archives Learn Lean Sigma
Comments are closed.