Root Cause Analysis Explained Lean Six Sigma

Lean Six Sigma Root Cause Analysis Rca Vative Root cause analysis (rca) is a key tool in continuous improvement, acting as a systematic approach to identify and tackle the underlying issues behind problems. rca aims not only to provide a temporary fix but to offer long lasting solutions by addressing the root causes. rca, such as the fishbone diagram, the 5 whys, and fmea. A root cause analysis (rca) is a problem solving method to identify the root causes of faults or problems. a factor is considered a root cause if removal from the problem fault sequence prevents the final undesirable event from recurring. short term actions are not profitable for the organization; thus, rca helps permanently eliminate the issues.

Root Cause Analysis Tools In Lean Six Sigma Root cause analysis seamlessly integrates into lean six sigma cultures demonstrating infrastructure capabilities enabling reliable prevention. however, any organization in search of elevating standards, systematizing enhancements, or diagnosing tricky recurring issues can benefit from instituting rca capabilities. 12. min. a six sigma root cause analysis is the long term solution your business needs for quality management. statistics and data analytics drive the methodology behind this approach that will get to the root of the problem. frontline workers and business owners alike strive for increased quality production. The lean six sigma bureau offers a comprehensive range of training programs, from yellow belt to master black belt, equipping you with the knowledge and expertise to master rca and all.conclusion:root cause analysis is a powerful tool for uncovering the underlying causes of process problems and driving continuous improvement. The goal of rca is to detect and resolve the root cause of a problem, thereby preventing the issue from recurring. in the context of lean six sigma, rca is used as a problem solving method to address inefficiencies and defects in a manufacturing process. it forms an integral part of the ‘analyze’ phase of the dmaic (define, measure, analyze.
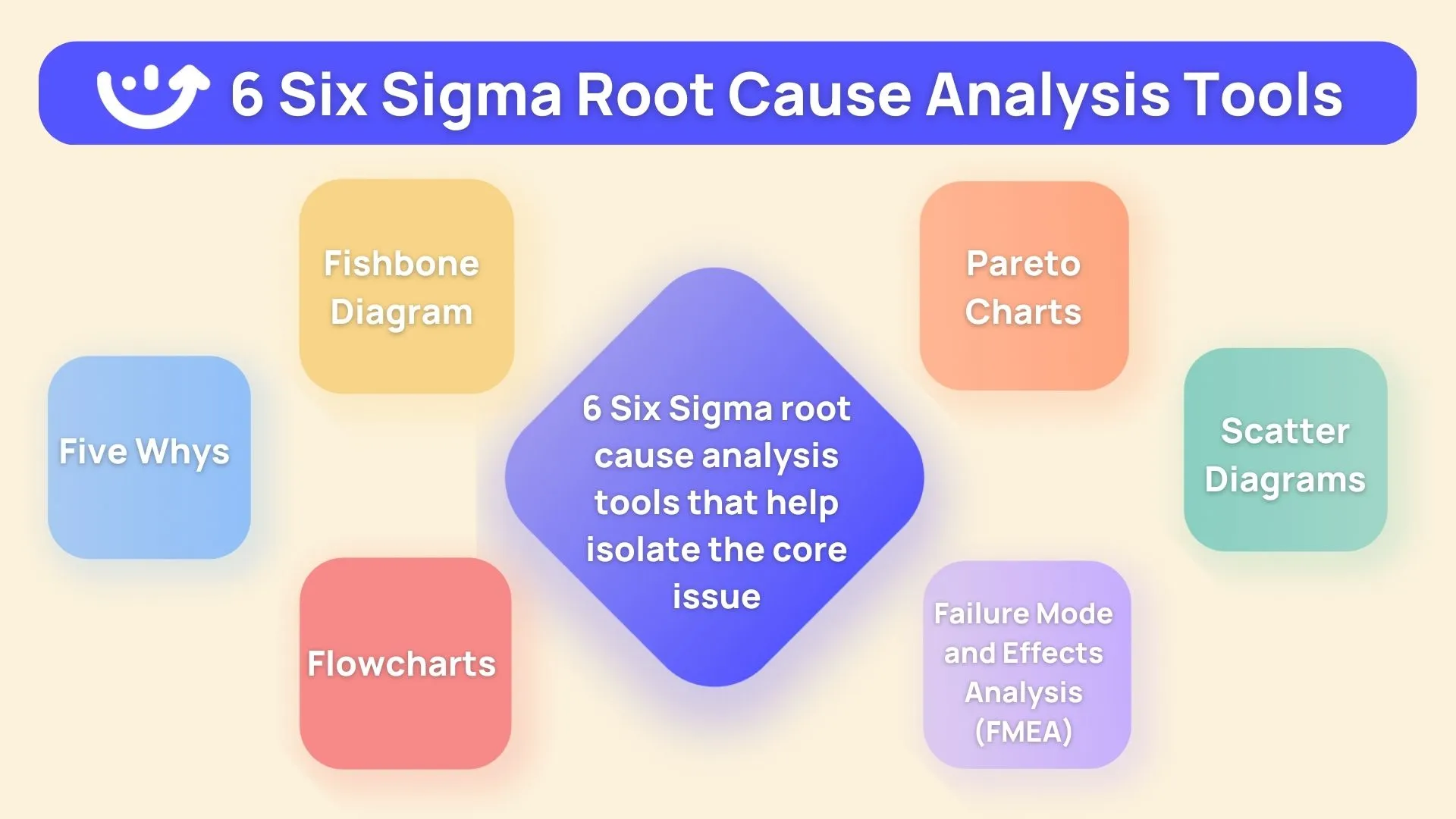
A Complete Guide To A Six Sigma Root Cause Analysis The lean six sigma bureau offers a comprehensive range of training programs, from yellow belt to master black belt, equipping you with the knowledge and expertise to master rca and all.conclusion:root cause analysis is a powerful tool for uncovering the underlying causes of process problems and driving continuous improvement. The goal of rca is to detect and resolve the root cause of a problem, thereby preventing the issue from recurring. in the context of lean six sigma, rca is used as a problem solving method to address inefficiencies and defects in a manufacturing process. it forms an integral part of the ‘analyze’ phase of the dmaic (define, measure, analyze. The fishbone diagram is a visual tool used in lean six sigma to identify root causes of problems. it resembles a fish skeleton, with the main problem at the head and potential causes branching off the spine into categories, facilitating a systematic approach to problem solving. also commonly known as a cause and effect diagram or an ishikawa. Root cause analysis (rca) is a way of identifying the underlying source of a process or product failure. as such, then the right solution can be identified. rca can progress more quickly and effectively by pairing an ishikawa diagram. you can also use the scientific method in the form of the well known plan do check act (pdca) cycle to.
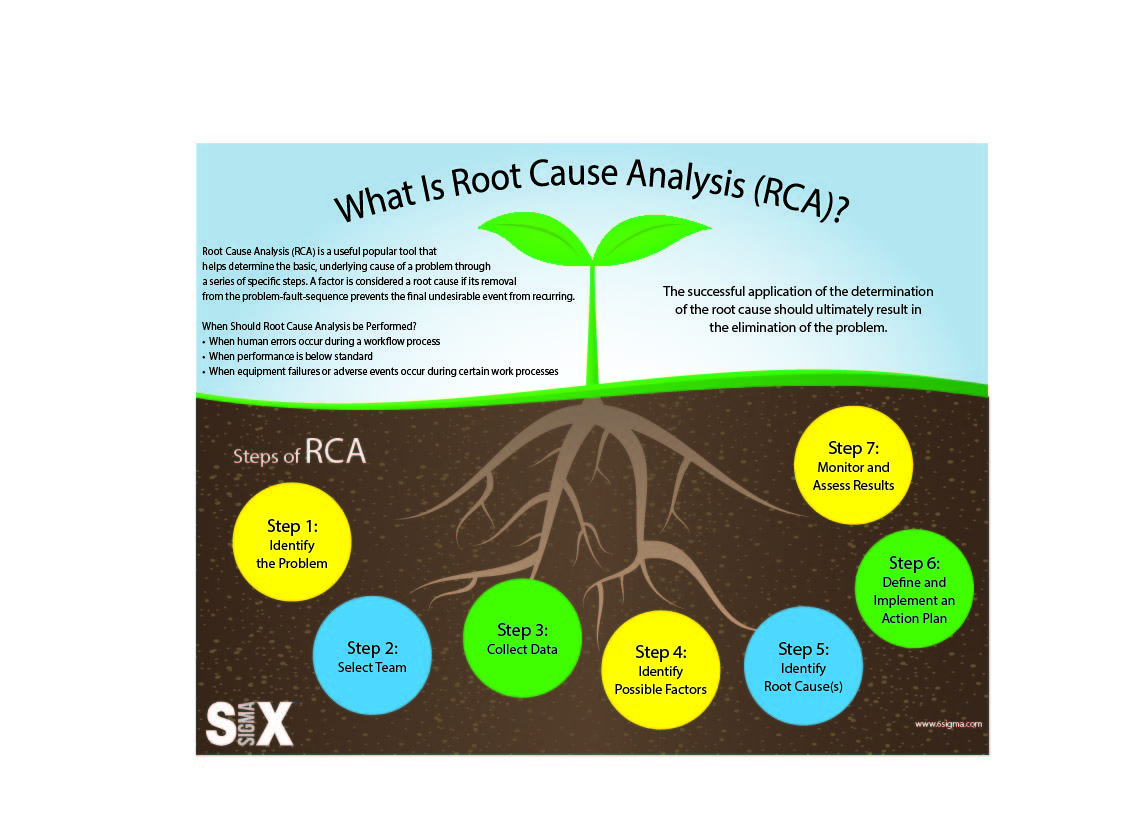
Infographic Root Cause Analysis Rca Lean Six Sigma The fishbone diagram is a visual tool used in lean six sigma to identify root causes of problems. it resembles a fish skeleton, with the main problem at the head and potential causes branching off the spine into categories, facilitating a systematic approach to problem solving. also commonly known as a cause and effect diagram or an ishikawa. Root cause analysis (rca) is a way of identifying the underlying source of a process or product failure. as such, then the right solution can be identified. rca can progress more quickly and effectively by pairing an ishikawa diagram. you can also use the scientific method in the form of the well known plan do check act (pdca) cycle to.
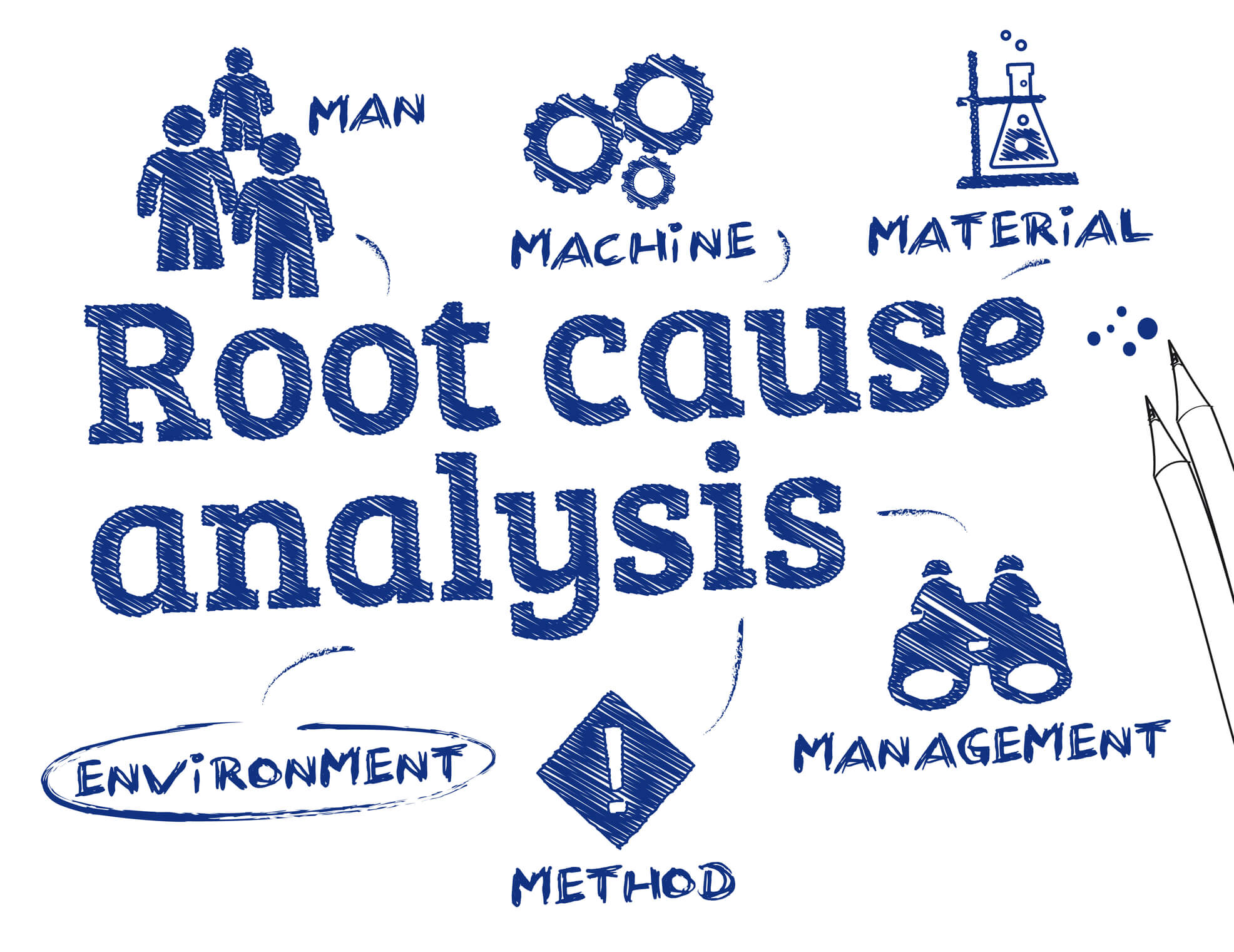
What Are The Tools Used For Lean Six Sigma Root Causeanalysis
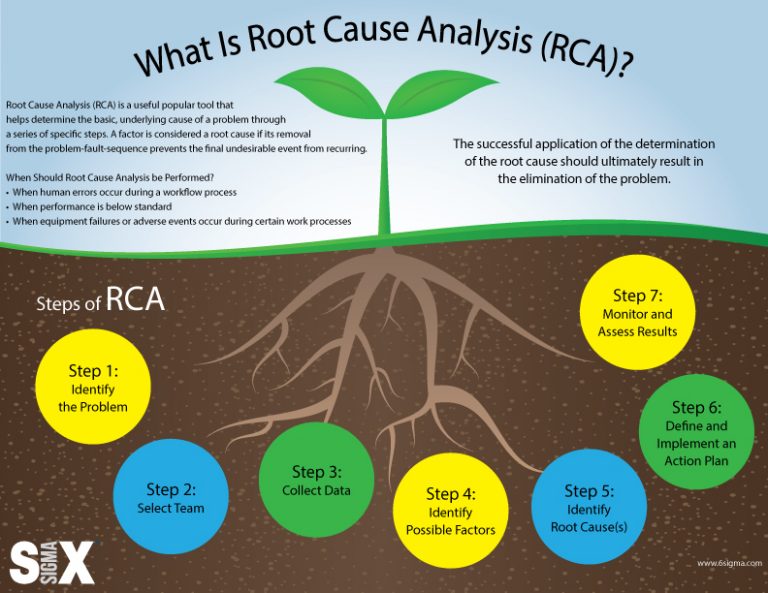
Infographic Root Cause Analysis Rca Lean Six Sigma
Comments are closed.