5 Minute Fix To Troubleshoot A Diaphragm Pumps

5 Minute Fix To Troubleshoot A Diaphragm Pump 5 Minute Fix To Here are six quick steps that can help you fix common problems during installation and operation. image 1. chemical transfer with air operated double diaphragm pumps (images and graphics courtesy of graco inc.) 1. check the inlet air line size and pressure. installing an air line that is too small is the most common mistake users make when. Follow these six easy steps to address common installation and operation problems.

5 Minute Fix To Troubleshoot A Diaphragm Pump Youtube Step 1. check the inlet air line size and pressure. installing too small of an air line is the most common mistake relating to an aodd pump. by using too small of an air line, you are starving the pump of the fuel compressed air it needs to operate at peak performance. double diaphragm pumps come in all shapes and sizes, based on the. A damaged diaphragm can lead to reduced flow rates. ensure that the pump’s air pressure is set correctly. insufficient air pressure can result in decreased flow. verify that the pump’s inlet and outlet sizes are appropriate for the desired flow rate. using a pump with inadequate size can lead to reduced performance. Top 5 tips for troubleshooting and repairing diaphragm pumps. you would agree that the pump can only be repaired once you identify the problem. you can perform troubleshooting in the following ways: extreme low or no pressure: at times, you may experience low or no pressure in the pump. these situations may be caused by insufficient rpm speed. Run the pump and adjust the control unit from bypass to the other settings to see if it is functioning. the pressure from the spray gun should change accordingly as you adjust the control valve. if the pump and regulating valve perform correctly when force primed, then it is almost certainly a suction plumbing issue.

5 Minute Fix To Troubleshoot A Diaphragm Pump Diaphragm Pump Top 5 tips for troubleshooting and repairing diaphragm pumps. you would agree that the pump can only be repaired once you identify the problem. you can perform troubleshooting in the following ways: extreme low or no pressure: at times, you may experience low or no pressure in the pump. these situations may be caused by insufficient rpm speed. Run the pump and adjust the control unit from bypass to the other settings to see if it is functioning. the pressure from the spray gun should change accordingly as you adjust the control valve. if the pump and regulating valve perform correctly when force primed, then it is almost certainly a suction plumbing issue. As usual, the first thing to do is to check if the suction line is clogged and clean the filter. one of the most common causes is cavitation, vapor bubbles form inside the fluid which implode and ruin the diaphragm. to avoid cavitation there are several useful tips, first of all you should not suck water from excessive depths (maximum 4 meters). Wet end. one clear indicator of diaphragm failure is exiting the pump through the exhaust. if this occurs, the pump needs to be shut down, isolated via suction and discharge valves, and removed from the system for repair. after the pump has been flushed and disassembled, you will want to inspect the diaphragms.
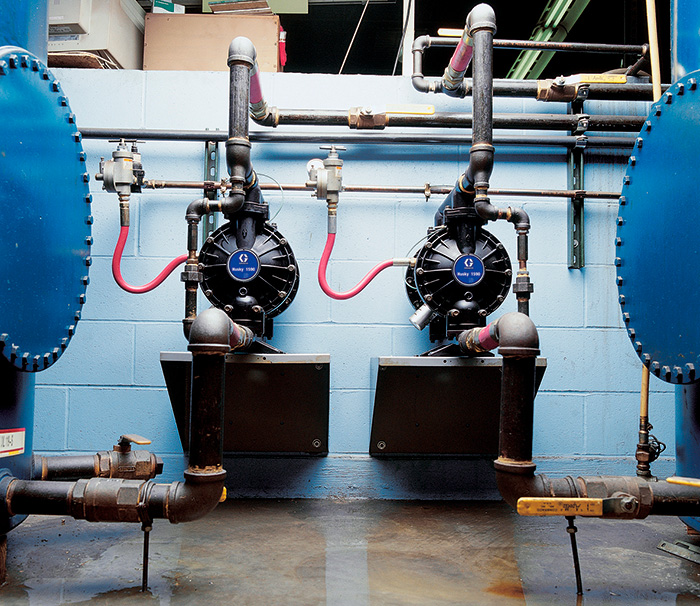
5 Minute Fix To Troubleshoot A Diaphragm Pumps As usual, the first thing to do is to check if the suction line is clogged and clean the filter. one of the most common causes is cavitation, vapor bubbles form inside the fluid which implode and ruin the diaphragm. to avoid cavitation there are several useful tips, first of all you should not suck water from excessive depths (maximum 4 meters). Wet end. one clear indicator of diaphragm failure is exiting the pump through the exhaust. if this occurs, the pump needs to be shut down, isolated via suction and discharge valves, and removed from the system for repair. after the pump has been flushed and disassembled, you will want to inspect the diaphragms.

5 Minute Fix To Troubleshoot A Diaphragm Pump Antlia Engineering
Comments are closed.